It’s a major contributor to climate change — the way buildings and roads are made with concrete. It’s also a problem that’s growing as more of the world develops. So the race has been on to find solutions for a material that’s responsible for roughly 8% of global carbon dioxide emissions. Now one California startup has developed a technology that reduces carbon dioxide in the making of cement and could have the potential to operate at large scale.
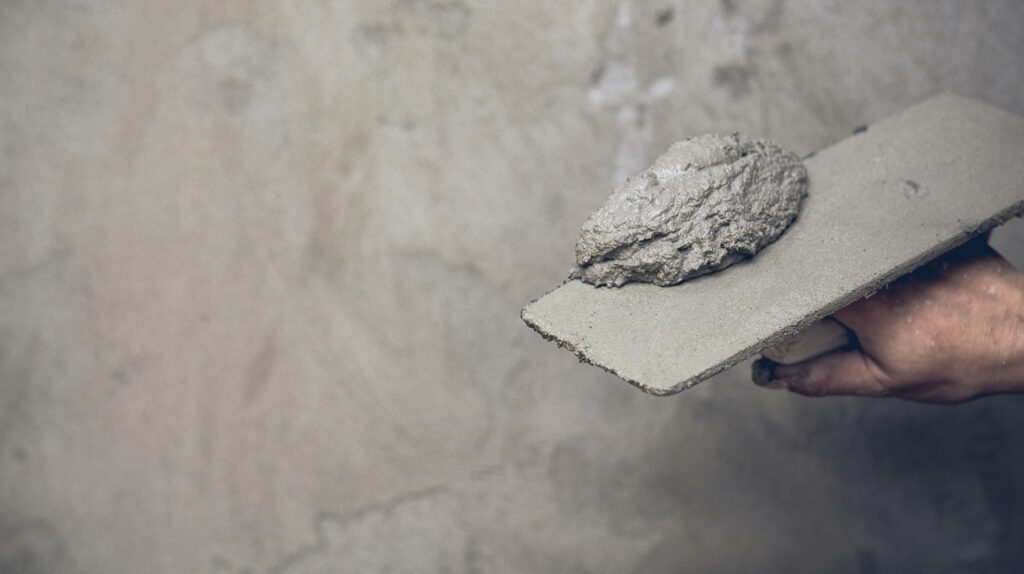
Fortera intercepts carbon dioxide exhaust from the kilns where cement is made and routes it back in to make additional cement. In its first effort at commercial scale, the technology is being added to a CalPortland facility in Redding, California, one of the largest cement plants in the western U.S. “Our target is about being a ubiquitous solution that can work really at any plant,” said Ryan Gilliam, Fortera CEO.
Initially Fortera will produce enough to mix with about one-fifth of CalPortland’s product in a blend that reduces carbon by about 10%. Gilliam said there is a strong demand for higher blends that reduce carbon by 40-50%, and for a pure product the company makes, which has 70% lower carbon. The first large sacks are scheduled to move out the door of the Redding plant the first week of May.
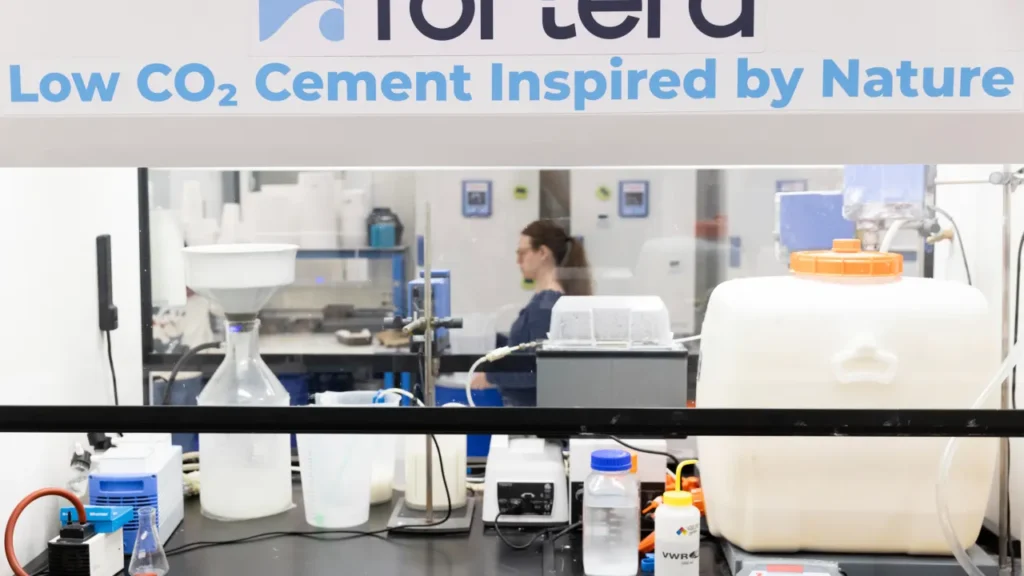
Fortera evolved in part out of an earlier company called Calera that was among the first to convert carbon dioxide into cement starting in 2007. It poured some 100 tons of its low-carbon cement into California office buildings and sidewalks but shuttered in 2014 due to financial challenges. Building on that knowledge, Gilliam founded Fortera in 2019 with several former Calera employees.
There is “pretty much a cement plant every 250 miles in the world,” he said, and most are located near a limestone quarry. Because it works with these existing plants and uses the same material the industry already uses, Fortera says its technology is an economically competitive option to quickly prevent carbon emissions from warming the planet. One difference from some other low-carbon cement and concrete efforts is it offers at least the possibility of being installed widely at cement plants instead of changing how the industry currently runs.
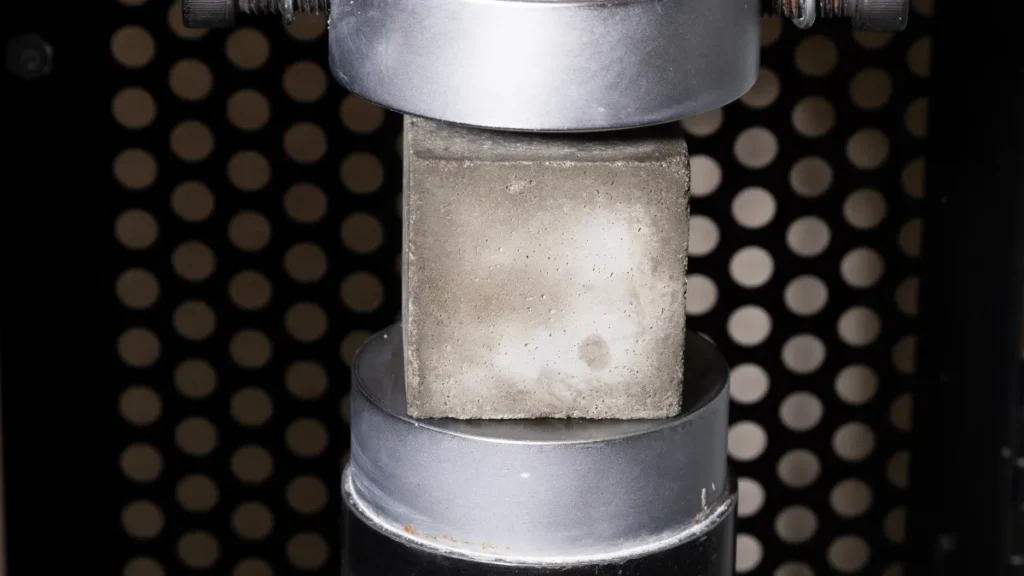
Fortera’s is one of many efforts to reduce the climate impact of concrete. The American Institute of Architects educates many of the world’s largest architecture firms about carbon emissions from building materials. Some jurisdictions including Vancouver, British Columbia have building standards that encourage lower-carbon concrete.
California passed a law in 2021 that requires the state’s Air Resources Board to develop a strategy for the state’s cement industry to reduce its greenhouse gas emissions by 40% by 2035 and achieve net zero by 2045.
The First Movers Coalition, an organization of more than 90 companies, has an initiative announced in 2021 to create greater demand for low-carbon cement through their immense buying power. The same year, 40 of the largest cement and concrete manufacturers announced a commitment to making concrete that does not contribute to climate change by 2050 through the Global Cement and Concrete Association. They agreed to reduce emissions from cement, fossil fuel use in manufacturing processes and to develop new ways to capture carbon. Concrete is the second-most used product on Earth, aside from water.
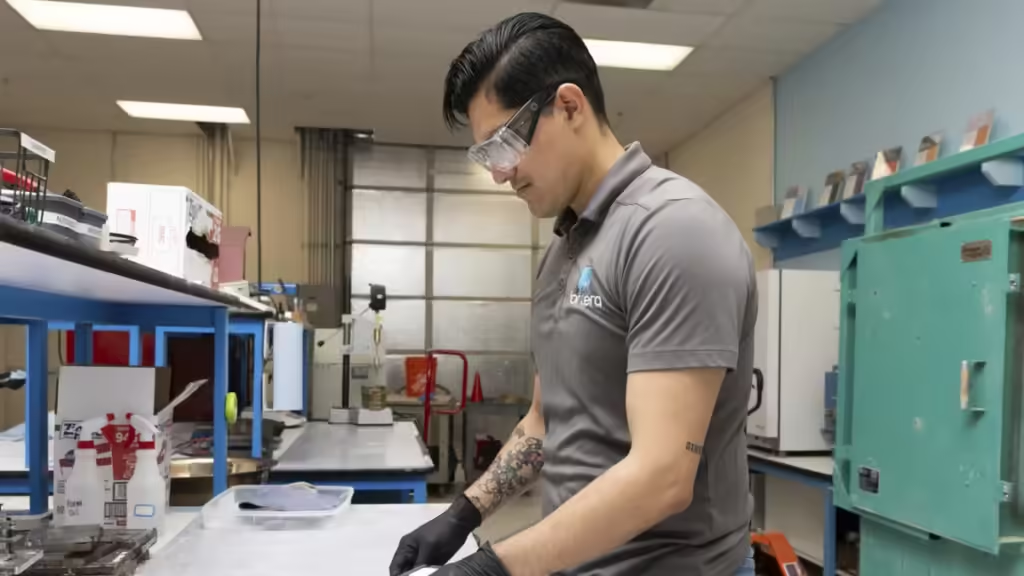
Cement makes up 10-15% of concrete by volume, but accounts for 88% of concrete’s considerable emissions. Other ingredients in concrete are sand, gravel, crushed stone and water. Manufacturing one ton of cement emits nearly one ton of carbon dioxide. There hasn’t been a simple replacement. “The societal benefits of concrete are absolutely immense… it’s the backbone of modern society,” said Thomas Guillot, CEO of the Global Cement and Concrete Association.
Other materials sometimes fail to compete because they are not as durable, can’t support as much weight, or can’t stand up as well to heat, he said. HOW FORTERA’S TECHNOLOGY WORKS Cement manufacturers heat kilns to about 2,500°F (1,400°C) to break down limestone and separate it into carbon dioxide and calcium oxide. Fortera’s process sucks the carbon dioxide out and pipes it into a machine where it is turned into a solid. Its technology works at around 1,800°F (1,000°C), which requires less energy and emits less carbon.
When the captured carbon dioxide is mixed with calcium oxide, it turns into a kind of limestone that becomes cement-like when wet. This product, which Fortera calls ReAct, is blended with other ingredients to make concrete. Fortera uses a 15% blend of ReAct in concrete because that is all that is allowed under existing industry standards that regulate material strength and durability.
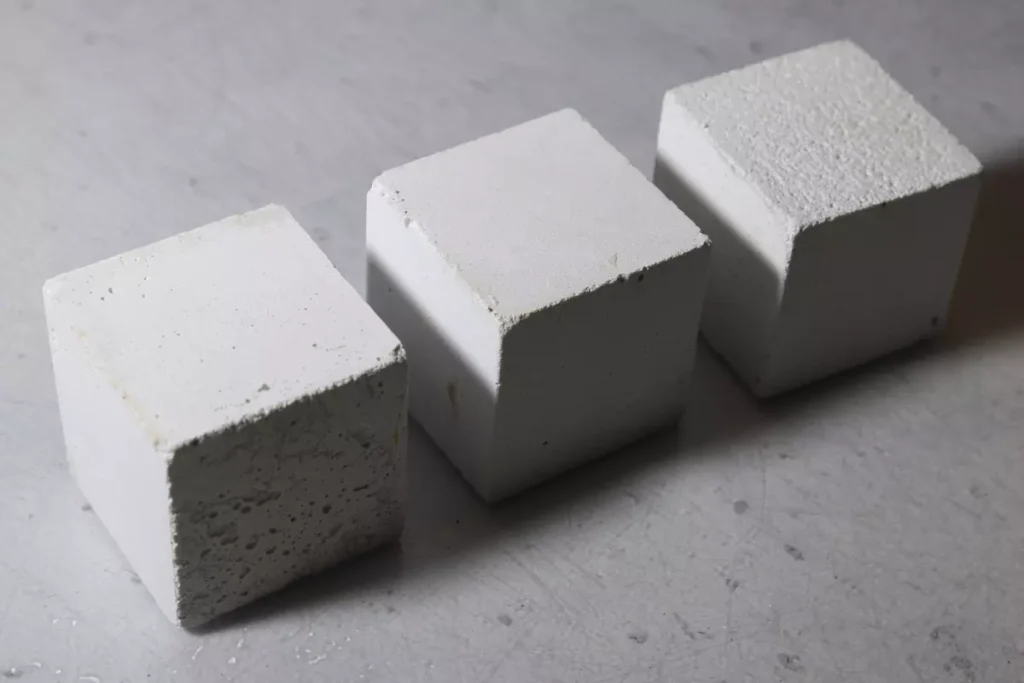
The company is trying to get a product that is 100% ReAct approved as a replacement for cement and says its testing has shown it can meet international requirements, but the regulatory process will take over five years. Some of the fastest-growing consumers of cement are in Southeast Asia and Africa, so global solutions are critical.
“The United States has to do what it can and be a leader to help other countries,” said Mike Ireland, president and CEO of the Portland Cement Association, the national trade association for U.S. cement manufacturers. “But we have to get the rest of the world, particularly the Global South, as they industrialize to leapfrog some of the technologies we had.” Carbon emissions from cement manufacturing is “an existential threat to the world and for our industry,” he said.